Cycling suits developed thanks to Artec's 3D technology
In the world of high performance cycling, speed is everything. A cyclist, to overcome the friction of the air, can use up to 90% of his physical efforts, therefore reducing this friction is essential to gain valuable time and increase the cyclist’s speed.
More than focusing on the bicycle, it makes more sense to focus on the cyclist in a broad sense: on the biomechanics in the various riding positions, on training, but above all on technical clothing. To meet these needs, Vorteq chose Artec 3D to develop the fastest cycling suits in the world.
The importance of ad hoc cycling suits
The suit remains the most aerodynamic piece a cyclist can wear. Not only that, this essential garment could reduce the level of friction, even below what it would be if the athlete were naked.
The cycling suit for professionals must reflect other important characteristics: comfort, lightness, high breathability. The personalization of a suit then turns out to be a key component. If made without customization, it may not adhere perfectly to the athlete, filling with wrinkles. And wrinkles or folds in fabrics are the worst enemies of aerodynamics, because they increase air resistance. Translated: loss of speed.
Seams and types of fabrics can drastically alter the final result of the suits. For this reason, choosing optimal raw materials plays a fundamental role.
Creating a suit that takes into account the shape of the body and the size of the cyclist remains of essential importance. The anatomy varies from body to body and adherence with such a level of customization cannot be found in any shop.
Artec Leo for the creation of customized cycling suits
The use of a 3D scanner was the answer on how to produce high-performance cycling suits.
Artec Leo by Artec 3D was the final choice, perfect for digitally capturing the athlete’s exact anatomy.
So Vorteq engineers turned to Artec Central Scanning, specialists in all aspects of 3D scanning. The experts recommended Artec Leo, a revolutionary portable 3D scanner with built-in touchscreen and data acquisition rates up to 80 fps. In addition to being completely wireless, Leo excels at capturing medium-sized objects such as people in minutes.
TotalSim, parent company of Vorteq, previously used a third-party boom scanner to scan race cars, bicycles, and other items, but that device was not suitable for scanning people, as needed for the task. of the creation of personalized suits. This is the reason why the choice of the scanner fell on Artec Leo.
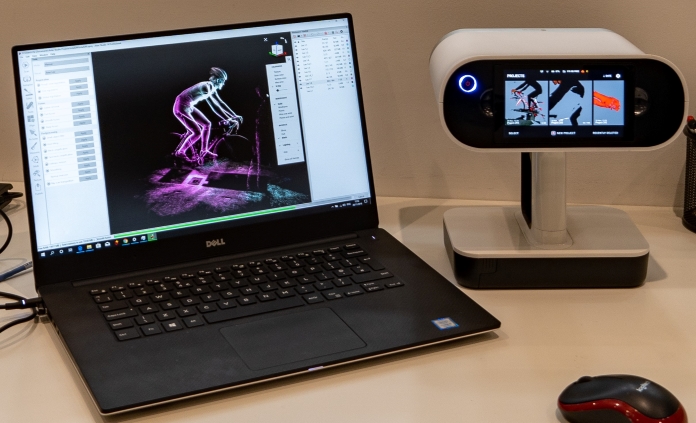
The flow of 3D scanning
Once the new Artec Leo was received, Vorteq engineers created a digital acquisition workflow, which consists of:
Let the cyclist enter the specially designed wind tunnel, mount his bicycle on a platform and in just 6 minutes Artec Leo “captures” the athlete from two positions in 3D, color and high precision / resolution. Another minute then to also capture the shoes from each side, to complete the anatomical scan.
“In ten minutes I can finish the work on a cyclist and proceed further. I have everything I need to design an anatomically accurate Vorteq suit that’s as fast as a bullet. There’s not the slightest chance that a second scan will be needed. ”Says Sam Quilter, metrology engineer.
The athlete is scanned thanks to Artec Leo, and once the 3D scans have been made, they move on to Artec Studio to process them. 3D Systems’ Geomagic Wrap is then used for 3D modeling. As a final step, the 3D model is exported to then make the cycling suit. From the start of the trial to the end it takes about 2 hours: “Impossible in the past, we weren’t even close to such a timeline,” continues Sam Quilter.
“As for the delivery of the completed cycling suit we need 2 days at the moment, but our goal is to be able to deliver the suits within 24 hours”, concludes Quilter.
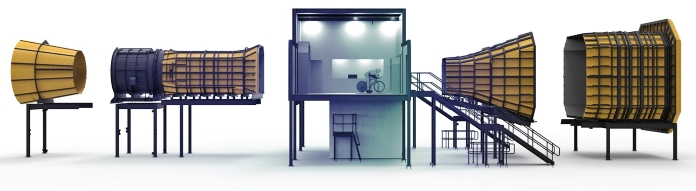
The advantages of Artec Leo
“When we make the cycling suits, we only take into consideration the 3D scans made with Leo, which are exact data and not measurements taken manually. Nothing is lost in the process, you don’t have to re-enter the measurements taken manually into the CAD system or a computerized drapery system. Even a small crease could compromise the success of the cycling suit mission, making our work useless “.
Furthermore, Artec Leo is completely wireless and acquires data in a super fast and accurate way at the same time.
A facilitated post-processing phase
The post-processing flow in Artec Studio is also simplified. Engineer Quilter adds that: “Leo makes things a lot easier for us. There are not many steps required in Artec Studio. I review the collected data, double-check everything, then use the Eraser tool to remove any unwanted bits. I usually keep the bike in the scan, as this is a great reference point for getting XYZ positioning and angle, then I go into the global registration, where I use the default settings because they work perfectly. Normally I don’t need to perform an Outlier Removal, because the data is already clean enough. Then I run Smooth Fusion and after a few other small tweaks I export it as an STL file for use in Geomagic Wrap. ”
In Geomagic Wrap, Quilter explains that instead “the Decimate tool is used to further decrease the number of triangles, and if I want to get rid of any wrinkles, which shouldn’t be in the scan, I switch to the Smooth command, which allows me to eliminate any imperfections, because athletes sometimes move their fingers during the scan. Once finished, we export everything as an OBJ file to be used in our drapery software ”.
Not just cycling suits
What if the athlete is miles away, or on the other side of the globe?
Vorteq has also thought of this. To create mannequins that exactly reproduce the athletes, thanks to Artec Leo, of course. These mannequins will be used to create ad hoc cycling suits, without the athletes having to go to the Vorteq offices.
Test, scan, model, create (even remotely), to always be available for your customers.